HVAC commissioning and validation
Maximize Your Pharmaceutical Operations with our Expert Commissioning Services
With our comprehensive commissioning services, we help you maximize the efficiency, productivity, and quality of your operations, while minimizing risk and reducing downtime.
Commissioning is a critical process in the pharmaceutical industry that involves verifying and documenting that equipment, facilities and utilities are fully operational, meet design specifications, and comply with regulatory standards. The goal of commissioning is to ensure that a facility is capable of producing high-quality pharmaceutical products consistently and reliably.
Our comprehensive list of the commissioning services offered
At our company, we take a comprehensive and collaborative approach to commissioning services, working closely with our clients to understand their specific needs and goals. We understand that commissioning is a critical phase in the lifecycle of a pharmaceutical manufacturing facility or system, and we bring a wealth of expertise and experience to ensure that the commissioning process is completed efficiently, effectively, and in compliance with regulatory requirements.
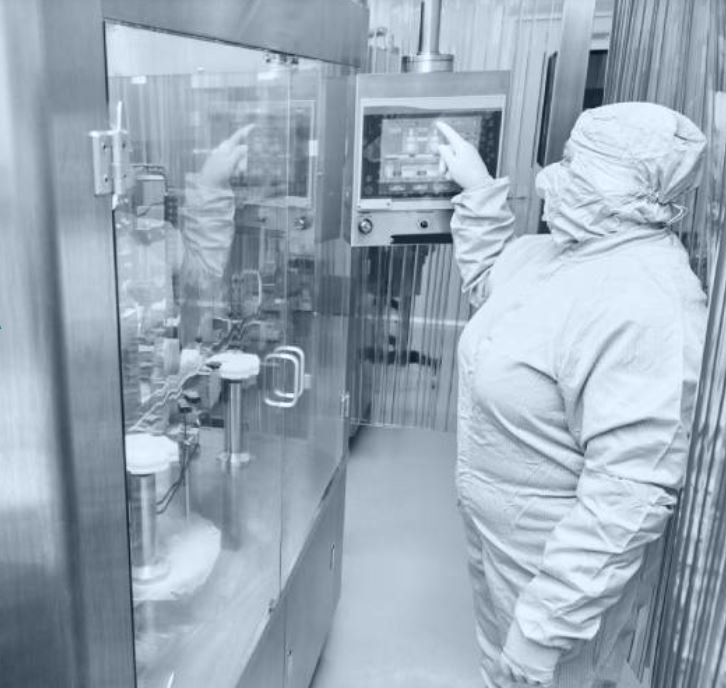
- Equipment commissioning
- Facility commissioning
- Validation services
- Commissioning project management
- Commissioning consulting
- Commissioning training
- Energy efficiency commissioning
- Commissioning for quality systems
- Commissioning for IT systems
- Commissioning for process automation
- Commissioning for cold chain logistics
The Process we follow for an effective pharma commissioning service
Our commissioning services for pharmaceutical companies in India follow a structured process that typically involves the following steps
Planning
The commissioning process starts with a detailed planning phase, where the scope of work is defined, timelines are established, and resources are allocated. This may involve working with the pharmaceutical company's engineering team, as well as external contractors and vendors.
Design review
Once the planning phase is complete, a design review is conducted to ensure that all equipment, facilities, and utilities are designed to meet the requirements of the pharmaceutical manufacturing process. This may involve reviewing design drawings and specifications, as well as conducting risk assessments and other analyses.
Installation and testing
After the design review is complete, the equipment and facilities are installed and tested to ensure that they operate as intended. This may involve a series of tests, including functional testing, performance testing, and integrated system testing.
Documentation
Throughout the commissioning process, all activities are documented to ensure that they meet regulatory requirements and quality standards. This may involve preparing detailed protocols, reports, and other documentation, as well as tracking and addressing any issues that arise.
Validation
Once the equipment, facilities, and utilities have been installed and tested, the final step is to validate the manufacturing process to ensure that it is capable of producing high-quality pharmaceutical products. This may involve conducting process validation studies, as well as ongoing monitoring and quality control activities.